In der heutigen digitalen Ära, in der Technologie und Automatisierung eine zentrale Rolle spielen, hat die Maschinendatenerfassung eine enorme Bedeutung erlangt. Doch warum ist die Erfassung von Maschinendaten so entscheidend?
In diesem Tech-Blog werden wir diese Frage beantworten. Und wir zeigen in 3 Schritten, wie Sie Ihre Maschinendaten erfassen.
Warum braucht es eine Maschinendatenerfassung in der Industrie 4.0?
Die Maschinendatenerfassung in der Industrie 4.0 umfasst die Erfassung und Analyse von Daten, die von verschiedenen Maschinen und Geräten in einer industriellen Umgebung generiert werden. Diese Daten werden genutzt, um Informationen über den Zustand der Maschinen, den Produktionsprozess und andere relevante Parameter zu gewinnen.
Neben den offensichtlichen Vorteilen wie der Überwachung von Maschinenleistung und Produktionsabläufen gibt es auch weniger offensichtliche Anwendungen der Maschinendatenerfassung, die oft übersehen werden. Einige dieser Aspekte sind:
- Steigerung der Effizienz: Durch die Erfassung von Maschinendaten werden Betriebsprozesse effizienter gestaltet, indem beispielsweise Engpässe erkannt und behoben werden.
- Verbesserung der Produktivität: Eine bessere Überwachung von Maschinen und Anlagen trägt dazu bei, dass Produktionsprozesse schneller und effektiver ablaufen.
- Reduktion von Ausfallzeiten: Mithilfe der MDE können Wartungsarbeiten und Reparaturen rechtzeitig geplant werden, um ungeplante Ausfallzeiten zu minimieren.
- Qualitätsverbesserung: Durch die Überwachung von Maschinendaten können mögliche Fehlerquellen frühzeitig erkannt und beseitigt werden, was zu einer höheren Produktqualität führt.
- Sicherheit: Eine bessere Überwachung von Maschinen und Anlagen kann dazu beitragen, Unfälle zu vermeiden und die Sicherheit am Arbeitsplatz zu erhöhen.
Was ist der Unterschied zwischen Betriebsdatenerfassung und Maschinendatenerfassung?
Betriebsdatenerfassung (BDE): Die Betriebsdatenerfassung bezieht sich auf die Erfassung und Verarbeitung von Daten über betriebliche Abläufe in einem Unternehmen. Sie umfasst eine breitere Palette von Informationen und kann neben den reinen Maschinendaten auch Daten über den Arbeitsfortschritt, die Mitarbeiterproduktivität, den Materialverbrauch, die Auftragsverwaltung, die Qualitätssicherung usw. umfassen. BDE konzentriert sich auf die Verwaltung und Steuerung der gesamten betrieblichen Prozesse, wobei auch nicht-maschinenspezifische Aspekte berücksichtigt werden.
Maschinendatenerfassung (MDE): Die Maschinendatenerfassung bezieht sich speziell auf die Erfassung von Daten, die direkt von Maschinen und Produktionsanlagen generiert werden. Sie konzentriert sich auf Informationen wie Produktionszähler, Stillstandszeiten, Auslastung, Produktionsgeschwindigkeit, Qualitätsdaten und ähnliches. MDE ist enger auf die Überwachung, Analyse und Optimierung der maschinenbezogenen Aspekte des Produktionsprozesses ausgerichtet.
In diesem Fachbeitrag sprechen wir im Wesentlichen über die Maschinendatenerfassung.
In 3 Schritten die Maschinendaten erfassen
Im Folgenden zeigen wir Ihnen einen praktischen und erprobten 3‑Schritte-Plan, wie Sie die Ziele Ihres MDE Projektes erfolgreich erreichen können.
Schritt 1: Vorbereitung und Planung:
- Identifizieren Sie die Maschinen, von denen Sie Daten erfassen möchten. Legen Sie fest, welche Art von Daten für Ihre Anforderungen relevant sind, z. B. Betriebsstunden, Temperatur, Leistungsaufnahme usw.
- Überprüfen Sie die vorhandene Infrastruktur, um sicherzustellen, dass die Maschinen mit Sensoren oder anderen Datenerfassungsgeräten ausgestattet werden können. Möglicherweise benötigen Sie spezielle Hardware oder Software, um die Datenerfassung durchzuführen.
- Definieren Sie klare Ziele für die Maschinendatenerfassung. Was möchten Sie mit den erfassten Daten erreichen? Mögliche Ziele könnten die Verbesserung der Produktionsleistung, die Reduzierung von Ausfallzeiten oder die Optimierung von Wartungsplänen sein.
- Lesen Sie hierzu auch unseren Beitrag: mit einem Solution Design Konzept den Grundstein legen.
Schritt 2: Installation der Datenerfassungseinrichtungen
- Beschaffen Sie die erforderlichen Sensoren oder Geräte zur Erfassung der gewünschten Daten. Stellen Sie sicher, dass sie mit den Maschinen kompatibel sind und die erforderlichen Informationen liefern können.
- Installieren Sie die Sensoren oder Datenerfassungsgeräte an den entsprechenden Maschinen gemäß den Herstelleranweisungen. Stellen Sie sicher, dass sie ordnungsgemäß angeschlossen sind und korrekt funktionieren.
- Konfigurieren Sie die erforderliche Software oder Firmware, um die Daten von den Sensoren zu erfassen und zu speichern. Legen Sie fest, wie oft die Daten erfasst werden sollen und wie sie gespeichert und verwaltet werden sollen.
Sprechen Sie uns an. Wir liefern Ihnen eine für Sie passende Lösung mit dem Schmid Engineering DataSErver.
Schritt 3: Umsetzung
- Richten Sie eine geeignete Datenbank oder ein Datenmanagementsystem ein, um die erfassten Maschinendaten zu speichern. Stellen Sie sicher, dass Sie ausreichend Speicherplatz und eine effiziente Datenstruktur haben, um die Daten effektiv zu verwalten.
- Implementieren Sie Analysetools oder Algorithmen, um die erfassten Daten zu verarbeiten und nützliche Informationen daraus abzuleiten. Dies kann die Überwachung von Maschinenzuständen, die Vorhersage von Ausfällen oder die Identifizierung von Optimierungspotenzialen umfassen.
- Nutzen Sie die gewonnenen Erkenntnisse, um Maßnahmen zu ergreifen und die Maschinenleistung zu verbessern. Dies können vorbeugende Wartungsmaßnahmen, Prozessoptimierungen oder andere Schritte sein, die auf dem ermittelten Bedarf basieren.
Wie werden Maschinendaten erfasst?
Maschinendaten werden in der Regel mithilfe verschiedener Sensoren und Instrumente erfasst, die an den Maschinen angebracht sind. Diese Sensoren können verschiedene physikalische Größen wie Temperatur, Druck, Geschwindigkeit, Vibrationen, Durchfluss usw. messen, je nach den spezifischen Parametern, die überwacht werden sollen.
Gängige Methoden zur Erfassung von Maschinendaten sind:
- Sensoren: Sensoren werden häufig verwendet, um Messungen an Maschinen durchzuführen. Beispielsweise können Temperatur‑, Druck‑, Schwingungs- oder Stromsensoren an Maschinen angebracht werden, um wichtige Daten zu erfassen.
- Programmierschnittstellen (APIs): Einige Maschinen verfügen über eine API, die es ermöglicht, Daten auszulesen. Durch die Verwendung von APIs können Entwickler spezielle Anwendungen schreiben, um Daten von der Maschine zu erfassen und zu analysieren.
- Manuelle Eingabe: In einigen Fällen müssen Daten manuell erfasst werden. Dies kann zum Beispiel der Fall sein, wenn die Maschine über keine Sensoren oder APIs verfügt und die Daten von einem Bediener erfasst werden müssen.
- Protokolldateien: Protokolldateien können auch verwendet werden, um Daten von Maschinen zu erfassen. Wenn eine Maschine über eine Protokollierungsfunktion verfügt, können die Daten in einer Datei gespeichert und später analysiert werden.
- Bildverarbeitung: In einigen Fällen können Maschinendaten auch durch Bildverarbeitung erfasst werden. Beispielsweise kann die Anzahl der Produkte, die von einer Maschine hergestellt wurden, durch die Analyse von Bildern erfasst werden.
Welche Produktionsdaten gibt es?
Produktionsdaten beziehen sich auf Informationen, die während des Produktionsprozesses erfasst werden. Diese Daten umfassen typischerweise verschiedene Parameter, die den Fortschritt, die Qualität und die Effizienz der Produktion überwachen und steuern. Produktionsdaten werden somit verwendet, um die Leistung der Produktionsanlagen zu analysieren, Engpässe zu identifizieren, Verbesserungspotenziale aufzudecken und die Produktionsabläufe zu optimieren.
Diese Produktionsdaten werden häufig in Echtzeit erfasst und in einem Leitrechner oder einem Manufacturing Execution System (MES) oder einem Manufacturing Operations Management (MOM) System gespeichert und analysiert.
Lassen Sie sich von den folgenden Aufzählungslisten inspirieren. Zu den typischen Parametern gehören:
- Stückzahl
- Durchlaufzeiten
- Störgrunderfassung
- Produktionssignal
- Maschinenstatus
- Temperatur
- Druck
- Geschwindigkeit
- Vibration
- Stromverbrauch
- Fehlercodes
- Durchfluss
- Zustandsüberwachung
Alte Maschine — neue Möglichkeiten
Bei einem Retrofit werden in der Regel veraltete Komponenten, Steuerungen oder Systeme durch modernere Komponenten ersetzt.
Weitere Parameter, die für eine Maschinendatenerfassung wichtig sind:
- Ölstand: Der Ölstand wird gemessen, um sicherzustellen, dass er innerhalb des vorgesehenen Bereichs bleibt und um den Schmierölbedarf zu ermitteln.
- Luftfeuchtigkeit: Die Luftfeuchtigkeit wird gemessen, um Korrosion und Schimmelbildung zu vermeiden.
- Luftdruck: Der Luftdruck wird gemessen, um sicherzustellen, dass er innerhalb des vorgesehenen Bereichs bleibt und um den Luftbedarf zu ermitteln.
- Geräuschpegel: Der Geräuschpegel wird gemessen, um sicherzustellen, dass er innerhalb des vorgesehenen Bereichs bleibt und um die Lärmbelastung für Mitarbeiter zu minimieren.
- CO2-Konzentration: Die CO2-Konzentration wird gemessen, um sicherzustellen, dass sie innerhalb des vorgesehenen Bereichs bleibt und um die Luftqualität zu überwachen.
- Abgasemissionen: Abgasemissionen werden gemessen, um sicherzustellen, dass sie innerhalb der gesetzlichen Vorschriften bleiben und um die Umweltbelastung zu minimieren.
- Spannung: Die Spannung wird gemessen, um sicherzustellen, dass sie innerhalb des vorgesehenen Bereichs bleibt und um den Strombedarf zu ermitteln.
- Leistung: Die Leistung wird gemessen, um sicherzustellen, dass sie innerhalb des vorgesehenen Bereichs bleibt und um die Effizienz zu optimieren.
- Position: Die Position von Maschinenteilen wird gemessen, um Bewegungen zu überwachen und um Fehler zu erkennen.
- Drehmoment: Das Drehmoment wird gemessen, um sicherzustellen, dass es innerhalb des vorgesehenen Bereichs bleibt und um die Belastung der Maschine zu überwachen.
- Beschleunigung: Die Beschleunigung wird gemessen, um sicherzustellen, dass sie innerhalb des vorgesehenen Bereichs bleibt und um Schwingungen zu minimieren.
- Frequenz: Die Frequenz wird gemessen, um sicherzustellen, dass sie innerhalb des vorgesehenen Bereichs bleibt und um die Steuerung von elektronischen Komponenten zu optimieren.
- Lichteinfall: Der Lichteinfall wird gemessen, um sicherzustellen, dass er innerhalb des vorgesehenen Bereichs bleibt und um die Beleuchtung von Arbeitsbereichen zu optimieren.
- Phasenverschiebung: Die Phasenverschiebung wird gemessen, um sicherzustellen, dass sie innerhalb des vorgesehenen Bereichs bleibt und um die Steuerung von elektrischen Komponenten zu optimieren.
- Magnetfeldstärke: Die Magnetfeldstärke wird gemessen, um sicherzustellen, dass sie innerhalb des vorgesehenen Bereichs bleibt und um elektromagnetische Interferenzen zu minimieren.
Folgende Schnittstellen, Fabrikate und Steuerungstypen unterstützen wir …
… mit unseren Dienstleistungen, dem SE Leitrechner und dem SE DataSErver. Nicht aufgeführte Schnittstellen entwickeln wir übrigens durch unsere produktionsnahe Softwareentwicklung auf Anfrage.
- OPC UA Client
- SPS_S7
- Heidenhain
- StringManipulation
- Beckhoff
- SEwatch
- Adam
- App (Smartwatch)
- ASCII Reader
- Cobotta
- Cognex
- Datenbanken
- Euromap63
- Focas
- FTP
- http Client
- INI
- KeyLogger
- Modbus TCP
- MQTT Broker & Client
- NumCNC
- OPC DA Client
- Serielle Schnittstelle (auch virtuell)
- VQS950
- Socket
- TCP Socket Server
- Webservice Client
- Webservice Server
- XML Modul
Dank der Firma Schmid Engineering konnten wir mit dem DataSErver sämtliche Fabrikate und Steuerungstypen anbinden.
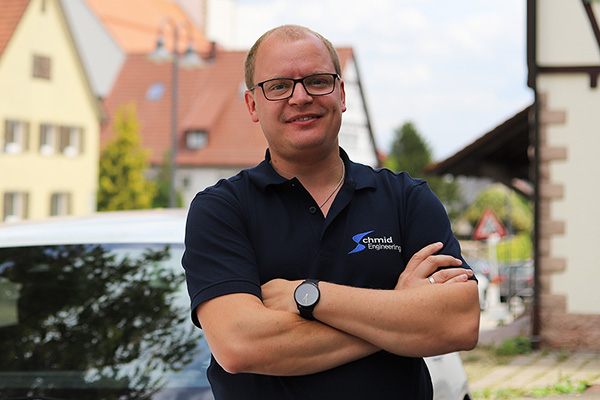